Development and production of high-performance materials for combustion chambers in gas turbines – using mixing technology from EIRICH
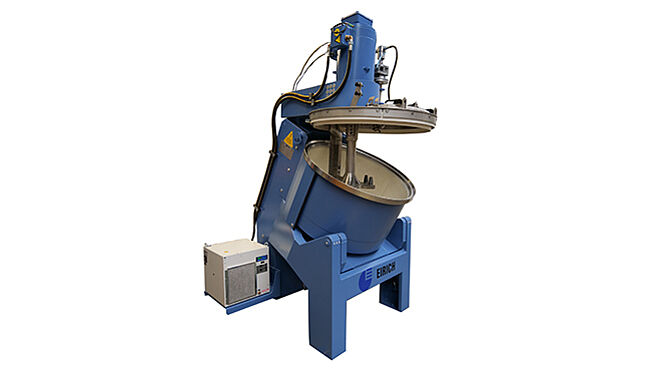
Electric current, or electric energy to be more precise, is at the heart of what makes a progressive, advanced society tick. Demand for electricity is constantly growing, not least due to our increasing usage of information technology and telecommunications. Electric energy is generated through conversion of other forms of energy. Although the profile of renewable energy sources like wind and solar power is constantly rising at present there is no getting away from the need to generate at least some of the energy we require from fossil fuels. We expect the highest efficiency from power stations, so that the energy available in the fuel is converted with minimal losses to heat and electricity. The high process temperatures demand high-performance materials. And when it comes to developing and producing these materials, companies and research institutions regularly opt for the best mixing technology available on the market – i.e. for mixing technol-ogy from Eirich.
When it comes to ensuring reliable energy supplies, conventional power stations still have an integral role to play. Modern power stations not only need to be highly efficient and offer low emissions, but we also expect operational flexibility from them. For stationary plants that are intended to serve as power station reserves, the ability to start up at very short notice is extremely important; depending on the requirements of the situation, power generation needs to be switched on or shut down very quickly. These power stations run with gas turbines that are operated with e.g. oil or natural gas. The plants offer efficiency levels of up to approx. 40%. Better efficiency of up to around 60% is achieved in combined gas and steam power plants (combined cycle power plants).
A gas turbine consists of a compressor, a combustion chamber, and a turbine. The compressor sucks in ambient air and directs it under high pressure into the combustion chamber, where fuel is injected and burned. The hot combustion gases flow at high speed into the turbine and cause it to spin, and this rotation is used to drive a power generator. In a combined cycle power plant, the still-hot exhaust gas is used to run a downstream steam turbine.
The combustion chambers are lined with high temperature-resistant ceramic elements. Combustion temperatures in excess of 1500°C demand high-performance refractory materials. The raw materials used in their production, such as aluminum oxide prepared in smelting or sintering processes, are hard (which is why they are also used as abrasive materials). The process of preparing the ceramic compounds requires a mixer with as few mixing tools as possible. Eirich invented such a mixer in 1924 as an evolution of the planetary mixer – with a rotating pan that transports the material being mixed to the mixing tools. This design layout keeps the transportation of the mix separate from the mixing process itself, meaning that fewer mixing tools are needed than with other mixers. As a result, the Eirich mixer is now the standard solution all around the world for the production of refractory materials. As well as laboratory mixers with a capacity of 1, 5, 10, and 40 liters, production mixers are available in sizes ranging from 75 to 3,000 liters. Larger sizes of mixer have not been needed to date in this industry. However, larger mixers are also available for other industries, such as a mixer with a usable volume of 12,000 liters for sintering processes.
Another feature that sets Eirich mixers aside from other mixers is the fact that the mixing tools can run faster without generating excessive friction or causing excessive wear on the mixing pan.
This means that an Eirich mixer can process any consistency – including, press bodies, plastic bodies, dry compounds (such as refractory concrete), or suspensions – all in a single machine.
All around the world, many companies are working on product improvements that are intended to extend the durability of materials for combustion chambers and improve the efficiency of power generating plants. Before they can be used in a production mixer, the first stage is normally to run trials in one of the test centers that are available at the different Eirich sites around the world. Here, experienced process engineers are on hand to help customers optimize prod-ucts using the customer’s own materials.
Further information:
Contact: Thomas Lansdorf, e-mail: thomas.lansdorf@eirich.de