Koblenz University of Applied Sciences decides for preparation of compounds for additive manufacturing for EIRICH mixer
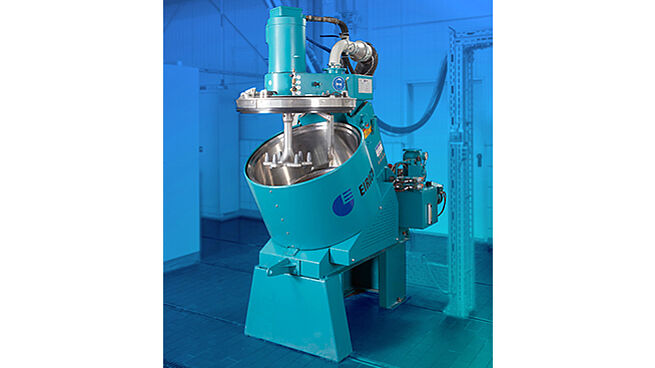
Additive manufacturing, usually referred to as 3D printing, has become increasingly important in many industries in recent decades. At the competence center for 3D printing of ceramics in Hoehr-Grenzhausen, Germany, refractory molded parts are to be produced for the first time. For the preparation of the mixes, the university has chosen the best available mixing technology and placed an order with Eirich to supply a mixer.
No other molding process for plastic, ceramic or metal components offers as much potential for cost savings as 3D printing - faster production, lower tooling costs, fewer steps and less scrap. There are also significant savings in prototyping and low-volume production. In addition, it is often possible to save materials and produce lighter parts. For example, 3D printing is already a standard process in the aerospace industry, e.g. for parts of turbines.
In ceramics, 3D printing has long focused on small items that were costly to produce conventionally. In the meantime, the process has successfully established itself in technical ceramics and dental ceramics. While the construction industry is now producing entire houses as demonstration objects for additive manufacturing, the ceramics industry still has some catching up to do when it comes to larger components and objects.
This has been recognized by the state government of Rhineland-Palatinate. As a result, the establishment of a center of competence for 3D printing of ceramics in Hoehr-Grenzhausen was funded in summer 2019 with around 5.3 million Euros, half of which comes from the European Regional Development Fund (ERDF) and half from the state budget. The center is being set up by the Research Institute for Inorganic Materials -Glass/Ceramics (FGK), Koblenz University of Applied Sciences and the University of Koblenz-Landau. The project will initially serve to develop an infrastructure and build up know-how for the additive manufacturing of inorganic non-metallic materials. These cover the entire range of ceramic materials - from silicate ceramics, refractories, technical ceramics and transparent ceramics to multi-material printing.
For the preparation of "3D refractory mixes" with a 75-liter mixer, the decision fell on Eirich for several reasons. The Koblenz University of Applied Sciences already has five Eirich mixers with useful volumes of 1, 5, 10 and 40 liters. Their performance is well known. Eirich mixers differ from other mixers in that a rotating mixing container transports the mix to the mixing tool. The transport of the mixing material is thus decoupled from the actual mixing process. High-speed tools located close to the floor or wall, which are therefore subject to high wear, are no longer required. This means that the mixing tools can run faster without causing excessive friction and wear on the mixing pan. Starting in 1924, these mixers replaced the kneader and muller mixers common at that time in the refractory industry. It was now possible to produce dimensionally accurate and highly refractory bricks with less clay, to mix non-plastic mixtures without grain size reduction, to use different materials in terms of mineralogical composition and grain size in one and the same mixture, and thus to develop and produce high-performance materials in a targeted manner. As a result, the Eirich mixer is now the worldwide standard in the refractory industry.
Another unique selling point of the Eirich mixer is its problem-free scale-up capability. Mixes are developed on small mixers; transfer to larger mixers is often problematic. During scale-up, the volume of the mix grows with the third power, but the wall areas of the aggregate grow only with the second power. With pusher mixers (such as ring trough and planetary mixers) and with throw mixers (such as horizontal mixers), additional tool sets are needed as the mixer gets larger; the power density in the mixing container changes. In the case of the horizontal mixer, there is also the fact that fast-running choppers are required to support the mixing process / to deagglomerate fines, the effect of which, according to literature data, cannot be scaled up. The situation is different with the Eirich mixer: In mixers between 1 l and 3000 l, only one mixing tool is required, the so-called rotor. The power input into the mixture is very precisely defined by the type of mixing tool, the tool speeds and the direction of rotation. The respective task defines these parameters, which then remain mostly unchanged during upscaling. Moreover, within one revolution of the vessel, 100% of the mix is moved by the tool; the mixer therefore mixes without dead zones in the mixer - and without segregation, which also allows longer mixing times if required. The system-related properties of the Eirich mixing technology thus enable the process parameters to be easily transferred to the production machines, and in most cases to go into production without renewed time-consuming adaptation work.
The new mixer, made of stainless steel, will be delivered in spring 2021. A special feature is that not only the rotor drive is designed with frequency converter speed control, but also the mixing pan. This creates additional degrees of flexibility in process design.
For Koblenz University of Applied Sciences, the new competence center means a further strengthening of the WesterwaldCampus in Hoehr-Grenzhausen as a strong research and innovative location. Hoehr-Grenzhausen is also home to ECREF - European Centre for Refractories gGmbH, which organizes the International Refractories Colloquium (ICR) in Aachen. 3D printing will provide the refractory industry with a technology that is economical and therefore forward-looking.
More information:
Contact: Markus Walter, E-Mail: markus.walter@eirich.de, Lee Klein, E-Mail: leeklein@hs-koblenz.de