EIRICH mixer for the University of Cambridge
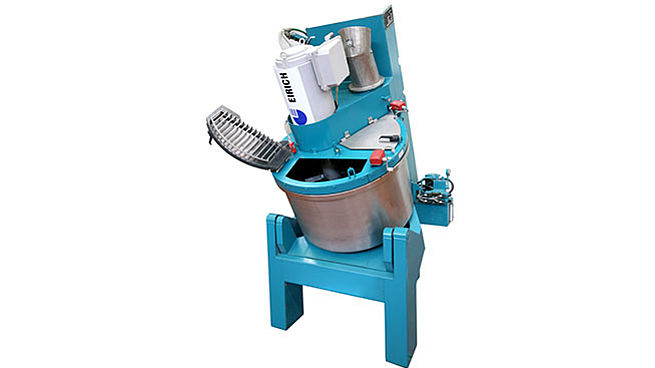
The performance of the compulsory mixer with rotating mixing pan and eccentrically arranged mixing tool, known as an Eirich mixer, has been described in many publications in various industries as the best available mixing technology. The best mixing results are achieved in combination with an intelligent control system ( „university control system” - developed in 2005). Parameters such as the mixing work done are recorded, which can also be preselected as required for the mixing process or its sub-steps. This combination of mixer and control system is particularly interesting for universities, because it allows knowledge to be gained that was previously not accessible. Today, more than 50 institutes worldwide use this technology. The University of Cambridge has now decided to use it as well.
The Department of Engineering at the University of Cambridge - one of the most prestigious and respected universities in the world - has recently constructed a new Civil Engineering building on the West Cambridge site, financed by the University of Cambridge and EPSRC (Engineering and Physical Sciences Research Council) through UKCRIC (UK Collaboratorium for Research on Infrastructure and Cities). The building will house the National Research Facility for Infrastructure Sensing (NRFIS) and - amongst others - the Laing O'Rourke Centre for Construction Engineering and Technology, the Centre for Smart Infrastructure and Construction, and the Research Groups on Structures and Geotechnical Engineering. The university has announced that the purpose-built facilities will enable cutting-edge research at a range of scales and will open up oportunities to work closely together with industry and other research institutes.
Cutting-edge research. For the university it was obvious that the best available mixing technology should be used. In an Eirich mixer, a further development of the planetary mixer invented by Eirich in 1906, the mixed material is transported by a rotating, inclined pan. Mixing is carried out by a fast-rotating mixing tool, known as the rotor, which has almost no contact with the bottom of the mixing pan and can therefore be operated at tool speeds of up to 30 m/s. In combination with a stationary wall / bottom scraper and two small bottom cleaning blades on the rotor, there is considerably less friction and wear than with conventional mixers. Reproducibility and reliable performance recording are possible with this setup. In addition, since the material is fully mixed within a single rotation of the pan, these mixers perform their mixing duties without any segregation at all.
The “university control system“ developed in collaboration between Eirich process engineers and academia - now offered as Premium Touch Control - registers and records all machine parameters (such as mixing pan speed, mixing tool speed, mixing pan and tool power consumption, mixing temperatures) and determines the relevant power input to the mix. The mixing procedure is thus documented and 100% reproducible. The power input can be used to visually track when the concrete is "ready".
Mixers with a usable volume of 40 litres or more are used in laboratories for construction material research. The results can be transferred to large production settings. The mixers have only one mixing tool (rotor) from 1 litres to 3000 litres and, hence, upscaling is therefore straighforward as the material flow conditions in the small mixer correspond to those with larger volumes.
The new mixing plant in Cambridge with a mixer type R09T (usable volume 150 litres, pan can be tilted for easy discharge) was put into operation in July of this year. The extended capabilities of Eirich's mixing technology will enable the Department of Engineering to gain new insights and help develop durable and sustainable materials.
More information:
Contact: Georg Henning, E-Mail: georg.henning@eirich.de