100 years of the Eirich mixing principle: A success story based on tradition and innovation
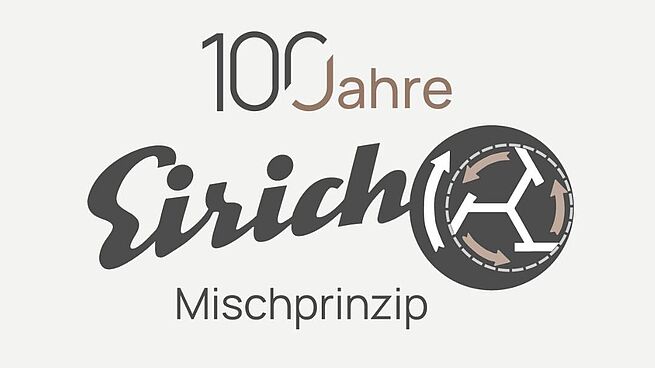
What was revolutionary 100 years ago is still regarded today as the best available technology in many respects. When the planetary mixer - an Eirich invention dating from 1906 - was no longer able to meet the increasing requirements of many sectors, the new “Eirich mixer” launched in 1924 proved itself to be talented at many kinds of applications. The patent gave rise to a mixing principle that changed entire industries and made the innovative end products that we know today possible in the first place. The Eirich intensive mixer has undergone minor and major developments ever since in response to constant new demands.
Hardheim, August 2024: With its focus on research and development, Eirich has carved out a reputation for itself over many decades as a partner and provider of innovative process engineering solutions for a large number of branches of industry. Eirich’s understanding of its customers and their problems has always been accompanied by process engineering know-how and a pioneering technological spirit.
A whole century of ideas
“We are proud of our success and our long history in what is such a dynamic market. Eirich demonstrates that tradition and innovation are not mutually exclusive, but rather build on each other and combine to deliver an absolute recipe for success. A lot of manufacturing companies rely on our technologies and value the durability of our machines, many of which have been in use for decades. We don't want to rest on our laurels, though: We’re constantly developing and are now also bringing digitalization into the production environment,” says Ralf Rohmann, managing partner of Eirich.
The first ring trough mixer was developed and patented in Hardheim in 1903. It was followed in 1906 by the planetary mixer, but the success story of the far more advanced Eirich mixing principle only began in 1924 with the construction for the first time of mixers with driven mixing pans. The mixers were introduced in many sectors as “Eirich counterflow mixers”.
In 1960 the company launched its fourth mixer generation, the countercurrent intensive mixer with an additional rotor – the first intensive mixer.
The fifth generation arrived in 1972. The mixers have an inclined rotating mixing pan, a stationary bottom/wall scraper, and a fast-turning rotor. This combination results in 100 % agitation of the material on every revolution of the mixing pan, which is what makes the Eirich mixing principle so efficient even today.
This was followed by intensive mixers with vacuum, heated, and cooled versions featuring all manner of wear protection in a range of sizes and with capacities extending from one liter to 12,000 liters. A 0.1 liter machine is in the development stage at the moment.
Know-how for cross-industry technology
Originally specializing in the construction and construction materials industry, the company has successfully expanded its mixing and processing solutions to many other sectors of industry as well. Today, Eirich intensive mixers are used not only in facilities making concrete and construction materials, but also in the chemical industry, environmental engineering, metallurgy, foundries, and ceramics, in the production of friction linings and carbon pastes, and in the manufacture of mineral fertilizers, foodstuffs and many other products. Over the years Eirich has established itself worldwide as a technology leader and contributed its expertise in over 150 sectors.
Significant progress across many industries
- Concrete industry:
The first Eirich mixer was developed in 1903 for the concrete industry, which was then still in its infancy. The company is able to meet the high demands placed on architectural and heavy-duty concrete in terms of quality and cost-effectiveness even now. It is constantly refining the mixing technology, delivering homogeneity, short batch processing times, high throughput rates, better fine distribution, and savings on coloring pigments and binders. - Ceramic industry:
The development of the planetary mixer in 1906 opened the door to ceramic applications. The main product at that time was refractory bricks. The development of the counterflow mixer and the subsequent intensive mixer meant that virtually all areas of ceramic production and the processing of carbon pastes were covered. Today the ceramic industry is one of the sectors hit hardest by rising energy prices, making innovative solutions essential. That is why Eirich developed the EcoPrep® process for generating low-cost, high-grade granules that are then compressed to form tiles or other ceramic products. This process saves up to 60 percent of the energy as well as additives and raw materials compared with conventional technology in spray towers. - Foundry industry:
With its molding sand mixers, Eirich has been a partner to foundries since 1925 and offers complete turnkey solutions for molding material preparation. The industry is now focused not only on high-grade production results, but also resource conservation and digitalization. Eirich has developed intelligent sand management technology that saves on raw materials and energy throughout the production cycle and also minimizes reject rates, even for castings. The EVACTHERM® process combines mixing, cooling, and bentonite activation in one machine under a vacuum atmosphere. The QualiMaster AT1 inline test unit monitors molding material quality in real time, ensuring a consistently high level of quality by identifying variances and learning how to counteract them. Data is also communicated with the downstream molding facility, enabling comprehensive production analyses and proactive molding material compositions. - Metallurgy:
The 1970s saw the first tentative tests conducted in collaboration with Lurgi (now Metso:Outotec) and the increasing use of Eirich mixers in iron ore pelletizing plants. Eirich won contracts because of the much better mixing quality it was able to offer compared with previous systems.
The next development stage for ever higher throughput rates came in the early 1990s with Eirich continuous mixers, culminating in 2006 in the type DW40, designed to process up to 1200 t/h of iron ore concentrate (equivalent to one complete freight train every hour).
Eirich was also able to achieve a higher level of production for sinter mixes because it could process much higher quantities of fines and ferrous residues.
The current trend is toward the processing of micropellets that are then refined further in hydrogen-based direct reduction and in the electric arc furnace. This enables us to make a major contribution to the decarbonization of the steel industry. - Battery industry:
Mixers from Eirich have been used for the processing of battery pastes for more than 80 years. They have set the pace in the development of both lead paste mixes for lead-acid batteries and depolarizers for dry cells. The machines with heavy kneaders were replaced in the 1960s by intensive mixers with high-speed mixing tools. With the subsequent introduction of vacuum technology, Eirich brought out a highly efficient solution for an absolutely homogeneous mixture, enabling the industry to experience a huge growth spurt. Today Eirich has established itself as a partner in the manufacture of lithium-ion batteries and offers new, resource-saving technologies for development labs all the way to giga-factories.
Customer proximity for new stimuli
“One of the key elements in the development of the company has been our dialog with existing and potential customers. This enables us to identify problems or new requirements and provide the appropriate technologies. Companies are constantly approaching us with inquiries or complex challenges they are facing in production. We sit down with them to develop new solutions that start in our own test center and ultimately end up in series production processes,” explains Stephan Eirich, CEO of Eirich. This ensures that the century-old history of the Eirich mixer is continuously updated. At the same time, the traditional company is paying particular attention to the digital transformation. High-tech and digital products are increasingly flowing into the industry solutions, from the online ordering of spare parts to AI-controlled quality assurance for the mixed end products.
This year Eirich has begun to tap into another new sector in the shape of the food and pharmaceutical industries. It has already presented three machines, the Cleanline C5, C40 and C400, that meet the explicitly high requirements for hygienic and contamination-sensitive areas.
“Thanks to its great flexibility, the rotating pan that Eirich invented is still ever-present even after more than 100 years. The pioneering work of the engineers at the time is set to remain the basis for innovation and progress – with the potential to take many other industries to a new level or even into a new age,” Eirich adds.