Destruction of grains during mixing of lightweight concrete
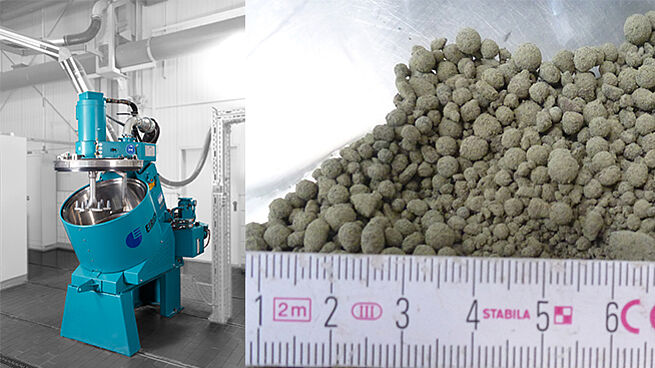
The use of lightweight concrete for the production of bricks and prefabricated parts is currently a major trend. The aggregates are offered in a range of grain sizes, and the amounts used in the recipes follow pre-defined particle size distribution curves. The particle size distribution curve determines the properties of the hardened concrete. During mixing of the concrete, lightweight aggregates can be broken down into smaller pieces through friction, and when pieces get trapped between the mixing tool and the wall of the vessel this can lead to the destruction of grains, causing the particle size distribution curve to be shifted and the properties of the concrete to be altered. On conventional forced-action mixers the processes also depend to a significant degree on the size of the mixer and the mixing time. Investigations have shown that Eirich mixers cause less grain destruction and enable more uniform production.
On lightweight concretes the lower bulk density in comparison to normal concrete is achieved through the addition of lightweight aggregates that have a high proportion of air pores and thus reduce the thermal conductivity of the material. These lightweight aggregates can take the form of naturally occurring minerals or synthetically produced mineral substances. Among these naturally occurring aggregates are natural pumice stone (from which bricks have been manufactured since the middle of the 19th century in the Neuwied Basin region of Germany) and lava slag/volcanic cinder. Today, synthetically manufactured lightweight aggregates are being used increasingly; examples of this include expanded clay or expanded shale. Natural rock is industrially processed in order to obtain the required porousness. The raw materials are finely ground, granulated, and foamed in rotary kilns. The end product is small, round rock pellets. As well as containing lots of air pores, these also have a largely closed surface, which means that they only absorb very little water. Today, scrap glass is ground down in a similar way to manufacture foamed glass, which has a particularly dense sinter skin.
In the relevant standards, a distinction is made between lightweight concrete with a dense structure and lightweight aggregate concrete with an open structure. In the case of the concrete with a dense structure, the particle size distribution curve can correspond to that of a normal concrete; the only difference is that lightweight aggregates are used instead of dense aggregates. With lightweight aggregate concrete with an open structure, which enables significantly lower bulk densities, the aggregate is chosen so that there are as many gaps as possible between the grains. The grains are coated with binding agent paste during mixing and stick together at the contact points during molding.
When the concrete is mixed, as the first step the lightweight aggregate is wetted with water – only then are cement and other powdery substances added. Liquid additives are added with the remaining water for mixing. The recommended minimum mixing time for lightweight concrete with a dense structure is 90 seconds after addition of all ingredients, compared to 30 - 60 seconds for normal concrete. It is documented in the literature that a demixing process is superimposed over every mixing process, which is why the mixing time in a conventional mixer cannot be extended arbitrarily. The best achievable mixing quality in any given situation is obtained after a certain length of time. If the mixing time is extended beyond this point, the quality of the mix will start to deteriorate.
When mixing lightweight concrete, the mixing quality is not the only factor – we also have to look at the destruction of grains that occurs during mixing. In conventional mixers the mixing tools run close to the bottom and side walls in order to move all of the materials and mix them in the process. Grains become trapped between the tools and the mixer housing and are broken down, resulting in a shift of the particle size distribution curve and increased water absorption. This effect also depends on the size of the mixer (larger mixers require more mixing tools) and the mixing time. This can only be remedied to a degree by increasing the gaps between the mixing tools and the mixer housing – after all, we don’t want anything to be left unmixed on the bottom of the mixing container.
When it comes to mixing lightweight concrete, there is another mixing technology that has proved its worth – the Eirich mixing system. In an Eirich mixer (a further development of the planetary mixer originally invented in 1906 by Eirich), the material being mixed is transported by an inclined, rotating container. Mixing is performed by a rapidly rotating mixing tool, which is referred to as the rotor, and this has virtually no contact with the bottom of the mixing pan. Together with a stationary wall/bottom scraper and two small bottom cleaning blades on the rotor, this significantly reduces friction and wear on the one hand and leads to less grain destruction on the other. And since the material is fully mixed within a single rotation of the pan thanks to the combined effects of the rotor and the bottom/wall scraper, these mixers perform their mixing duties without any demixing at all. The dependency of grain destruction on the size of the mixer is also greatly reduced. Series ‘R’ Eirich mixers only have one moving mixing tool – whether at a size of 1 liter or 3000 liters. Having fewer tools means that less of the material being mixed gets trapped, thus resulting in less destruction of grains. If there are fewer tools, this also means that upscaling is significantly simpler.
If you are interested in finding out more, test centers are available at all Eirich sites where the advantages of this superior mixing technology can be demonstrated.
Further information:
Contact: Stefan Berberich, e-mail: stefan.berberich@eirich.de