Keeping a close eye on everything thanks to digitalization
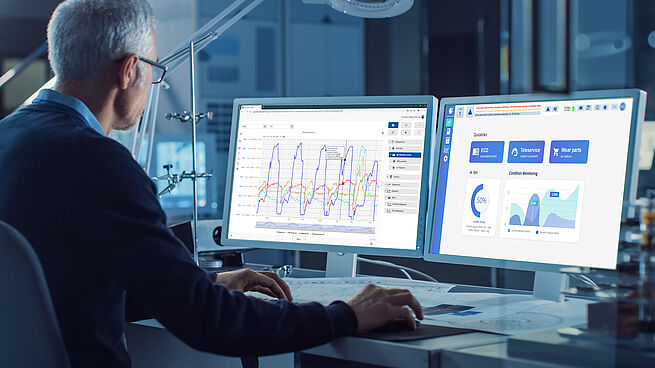
Eirich presents digital solutions for increased efficiency in service and production plants
With the onset of the era of Industry 4.0, digitalization is rapidly gaining momentum in the industry with intelligent networking of machines and lines. This digital transformation is enabling companies to open up new ways to control and organize the entire value chain. The long-established company Maschinenfabrik Gustav Eirich has developed a range of digital solutions for Lifecycle Services and Process Analytics to boost efficiency and streamline production processes.
Hardheim, January 2022: Many companies see digitalization as a key step for future success, and as a result they are attempting to optimize their processes in order to strengthen their own market position. For the family-run company Maschinenfabrik Gustav Eirich, the optimization of production processes and intelligent networking of production lines is a step toward more efficiency and greater sustainability. This creates flexible manufacturing structures, which play an incredibly important role in such a dynamic market. With its digital product portfolio, Eirich has also taken the topic of closeness to the customer to the next level: From fast ordering of spare parts to technical support provided by Eirich personnel, the company is aiming to offer customers even better service and barrier-free accessibility via its digital offerings.
Stephan Eirich runs the company now as CEO in the fifth generation of family ownership, and his focus is now on digitalization. He believes that digital transformation is a natural evolution for the industry: “How can we ensure that a preparation system we deliver to a customer today will continue to operate in the optimum range, without the customer needing to rely on the input and experience of experts – who are becoming increasingly more difficult to find? It is up to the machine supplier to implement this knowledge in the system right from the start. We see this as a great opportunity and believe we owe it to our customers. With Lifecycle Services and Process Analytics we offer our core industries genuine added value to help make production processes more reliable and more sustainable in the long run.”
Lifecycle Services enable transparent servicing – from real-time monitoring of lines to maintenance services based on augmented reality. The solutions focus on optimizing machine downtime and minimizing line outages:
- myEirich
With the aid of the electronic spare parts catalog from Eirich, customers can access visual models that enable them to intuitively identify installed components themselves. The shopping basket is the final link in the ServiceExpert ECD software – machine and line components that are required are simply added to the basket, and the order is placed directly by e-mail. In the myEirich application, customers can track the progress of a service order in real time and monitor its dispatch status live.
- Condition Monitoring
With this system, physical parameters are measured and analyzed to determine the current status and condition of a machine. Sensors supply data in real time. Continuous data analysis highlights trends and identifies possible damage to components before failure actually occurs. Crashes, bearing damage, imbalance, gearing faults, and wear are all detected early on and displayed. This allows the customer to order replacement parts in good time or contact the Service department before the machine fails – without having to allow for waiting times before service engineers can visit.
- Teleservice
Online service without service technicians present on-site – with remote servicing and remote diagnostics. The automatic collection and analysis of machine and process data means that faults can be isolated and located remotely. Once approved by the customer, measures can be put in place immediately to remedy faults, and customized software updates can be implemented without a presence on site.
- EIRICH-AR-Services
With the aid of augmented reality, specialists can gain an overview of the current status and condition of the system using a smartphone camera and smart glasses. Thanks to advanced 3D object tracking, arrows, notes, and markings can be superimposed on the display to make it easier for the user to follow the instructions of the expert. This maximizes productivity, reduces downtime and – more than anything – saves time and money.
With digital tools for Process Analytics, Eirich offers optimization solutions that safely and reliably improve production processes. - QualiMaster mit EIRICH ProView
The individual QualiMaster systems are a guarantee of quality in their relevant fields of application. The system continuously and automatically takes samples from the material being mixed, measuring the properties of the material in a range of ways. The ProView software visualizes and analyzes the measured data. With exceptional user friendliness, an incredibly clear visual presentation of the information and an array of adjustment options, this system offers users a wide range of options for monitoring and controlling engineering processes. The results can be analyzed by experts or with the aid of artificial intelligence so that subsequent batches can be successively improved.
This boosts quality and hugely reduces waste, making your production more stable and more efficient. QualiMaster systems are already available for optimizing molding material properties, moisture content, consistency, and flow properties as well as for optimizing the production of granulates.
For more information please visit: www.eirich.com/en/digital-solutions